Welcome to Ningbo Huarui Automation Equipment Co., Ltd.!

Company Culture
Hydraulic cylinder
Click Count: 8035
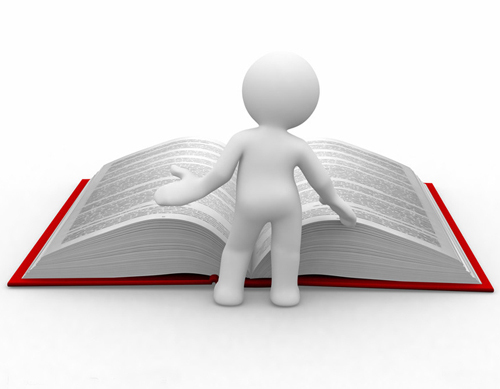
From Wikipedia, the free encyclopedia
The hydraulic cylinders on this excavator control the machine's linkages.
A Hydraulic cylinder (also called a linear hydraulic motor) is a mechanical actuator that is used to give a unidirectional force through a unidirectional stroke. It has many applications, notably in construction equipment (engineering vehicles), manufacturing machinery, and civil engineering.
Parts of a hydraulic cylinder[edit]
A hydraulic cylinder consists of the following parts:[1]
Cylinder barrel[edit]
The main function of cylinder body is to hold cylinder pressure. The cylinder barrel is mostly made from a seamless tube. The cylinder barrel is ground and/or honed internally with a typical surface finish of 4 to 16 microinch. Normally hoop stress is calculated to optimize the barrel size.
Cylinder base or cap[edit]
The main function of the cap is to enclose the pressure chamber at one end. The cap is connected to the body by means of welding, threading, bolts, or tie rod. Caps also perform as cylinder mounting components [cap flange, cap trunnion, cap clevis]. Cap size is determined based on the bending stress. A static seal / o-ring is used in between cap and barrel (except welded construction).
Cylinder head[edit]
The main function of the head is to enclose the pressure chamber from the other end. The head contains an integrated rod sealing arrangement or the option to accept a seal gland. The head is connected to the body by means of threading, bolts, or tie rod. A static seal / o-ring is used in between head and barrel.
Piston[edit]
The main function of the piston is to separate the pressure zones inside the barrel. The piston is machined with grooves to fit elastomeric or metal seals and bearing elements. These seals can be single acting or double acting. The difference in pressure between the two sides of the piston causes the cylinder to extend and retract. The piston is attached with the piston rod by means of threads, bolts, or nuts to transfer the linear motion.
Piston rod[edit]
The piston rod is typically a hard chrome-plated piece of cold-rolled steel which attaches to the piston and extends from the cylinder through the rod-end head. In double rod-end cylinders, the actuator has a rod extending from both sides of the piston and out both ends of the barrel. The piston rod connects the hydraulic actuator to the machine component doing the work. This connection can be in the form of a machine thread or a mounting attachment....
Seal gland[edit]
The cylinder head is fitted with seals to prevent the pressurized oil from leaking past the interface between the rod and the head. This area is called the seal gland. The advantage of a seal gland is easy removal and seal replacement. The seal gland contains a primary seal, a secondary seal / buffer seal, bearing elements, wiper / scraper and static seal. In some cases, especially in small hydraulic cylinders, the rod gland and the bearing elements are made from a single integral machined part.
Seals[edit]
The seals are considered / designed as per the cylinder working pressure, cylinder speed, operating temperature, working medium and application. Piston seals are dynamic seals, and they can be single acting or double acting. Generally speaking, Elastomer seals made from nitrile rubber, Polyurethane or other materials are best in lower temperature environments, while seals made of Fluorocarbon Viton are better for higher temperatures. Metallic seals are also available and commonly use cast iron for the seal material. Rod seals are dynamic seals and generally are single acting. The compounds of rod seals are nitrile rubber, Polyurethane, or Fluorocarbon Viton. Wipers / scrapers are used to eliminate contaminants such as moisture, dirt, and dust, which can cause extensive damage to cylinder walls, rods, seals and other components. The common compound for wipers is polyurethane. Metallic scrapers are used for sub zero temperature applications, and applications where foreign materials can deposit on the rod. The bearing elements / wear bands are use to eliminate metal to metal contact. The wear bands are designed as per the side load requirements. The primary compounds for wear bands are filled PTFE, woven fabric reinforced polyester resin and bronze.
Other parts[edit]
- Cylinder base connection
- Cushions
Single acting vs. double acting[edit]
For more details on this topic, see Single- and Double-acting cylinder.
- Single acting cylinders are economical and the simplest design. Hydraulic fluid enters through a port at one end of the cylinder, which extends the rod by means of area difference. An external force or gravity returns the piston rod.
- Double acting cylinders have a port at each end, supplied with hydraulic fluid for both the retraction and extension.
Hydraulic cylinder designs[edit]
There are primarily two styles of hydraulic cylinder construction used in industry: Tie rod style cylinders and welded body style cylinders.
Tie rod cylinder[edit]
Tie rod style hydraulic cylinders use high strength threaded steel rods to hold the two end caps to the cylinder barrel. This method of construction is most often seen in industrial factory applications. Small bore cylinders usually have 4 tie rods, while large bore cylinders may require as many as 16 or 20 tie rods in order to retain the end caps under the tremendous forces produced. Tie rod style cylinders can be completely disassembled for service and repair.
The National Fluid Power Association (NFPA) has standardized the dimensions of hydraulic tie rod cylinders. This enables cylinders from different manufacturers to interchange within the same mountings.
Welded body cylinder[edit]
Welded body cylinders have no tie rods. The barrel is welded directly to the end caps. The ports are welded to the barrel. The front rod gland is usually threaded into or bolted to the cylinder barrel. This allows the piston rod assembly and the rod seals to be removed for service.
A Cut Away of a Welded Body Hydraulic Cylinder showing the internal components
Welded body cylinders have a number of advantages over tie rod style cylinders. Welded cylinders have a narrower body and often a shorter overall length enabling them to fit better into the tight confines of machinery. Welded cylinders do not suffer from failure due to tie rod stretch at high pressures and long strokes. The welded design also lends itself to customization. Special features are easily added to the cylinder body. These may include special ports, custom mounts, valve manifolds, and so on.
The smooth outer body of welded cylinders also enables the design of multi-stage telescopic cylinders.
Welded body hydraulic cylinders dominate the mobile hydraulic equipment market such as construction equipment (excavators, bulldozers, and road graders) and material handling equipment (forklift trucks, telehandlers, and lift-gates). They are also used in heavy industry such as cranes, oil rigs, and large off-road vehicles in above-ground mining.